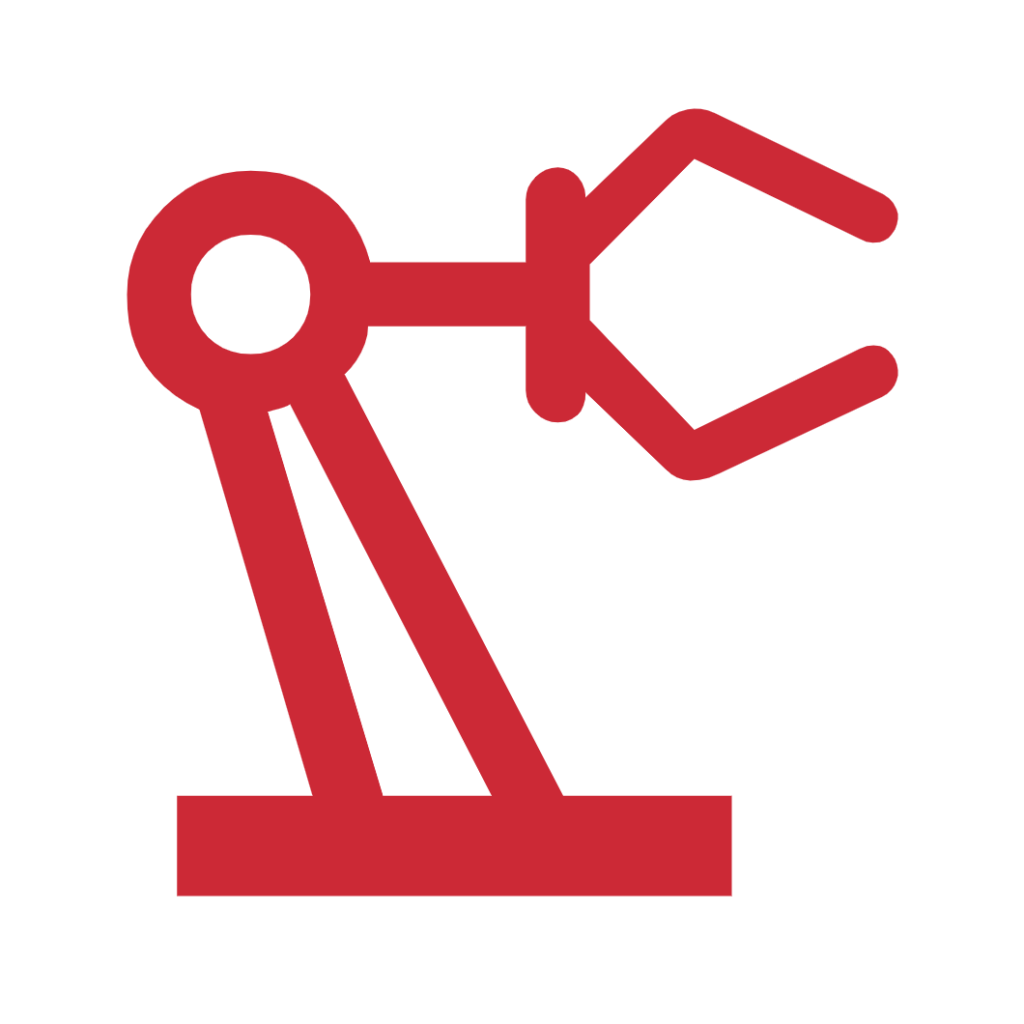
Advanced process analysis and optimization with discrete event simulation
A discrete event simulation is a modeling technique that analyzes the behavior of a complex system over time, focusing on specific events that cause changes in state, enabling the optimization of processes and the prediction of the impact of various decisions or operational configurations:
Evaluation of the effectiveness of modifying, adding, or removing machinery within the system to optimize performance and productivity.
In-depth assessment of the consequences of potential changes to work shift scheduling, ensuring alignment with operational goals.
Calculation of the most efficient route for forklifts to enhance both speed and fuel consumption, thereby improving overall logistics.
Detailed analysis of the potential impact of dismissing an operator with specialized technical skills, including the assessment of replacement needs and training requirements.
Calculation of the long-term consequences associated with altering key production process parameters, ensuring informed decision-making.
Identification of machine criticality and system bottlenecks, providing actionable insights to enhance overall system throughput and reliability.
CASE 1) RAW MATERIAL STORAGE SIZE
A major company in the poultry industry needed to determine whether the designated space for daily incoming raw materials (live birds) was adequate to meet production demands while also allowing room for unloading trucks upon arrival.
I conducted a comprehensive analysis of the production process and, through simulation, determined that the available space was sufficient.
Under normal operating conditions, the space would be occupied at an average of 70% of its total capacity.
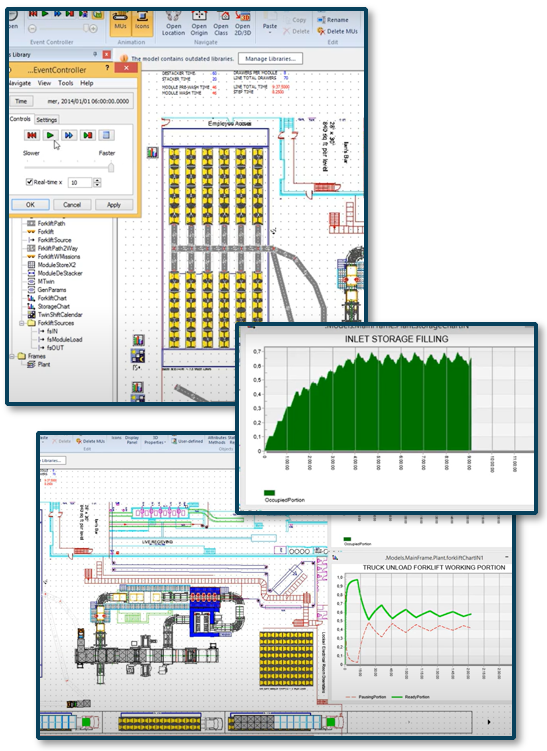
CASE 2) MINIMIZING TIME LOSS IN WALKPATHS
An Italian manufacturing company operating under the Job Shop production model requested an analysis of their plant layout to optimize the transportation paths of semi-finished products between various stations.
I conducted a thorough analysis of the processes and, through a discrete event simulation, found that in the best-case scenario, the client would achieve a reduction in walking time of less than 2%.
Given these findings, I advised against proceeding with the operation, as it would have caused months of delays and inefficiencies without delivering any significant benefits.
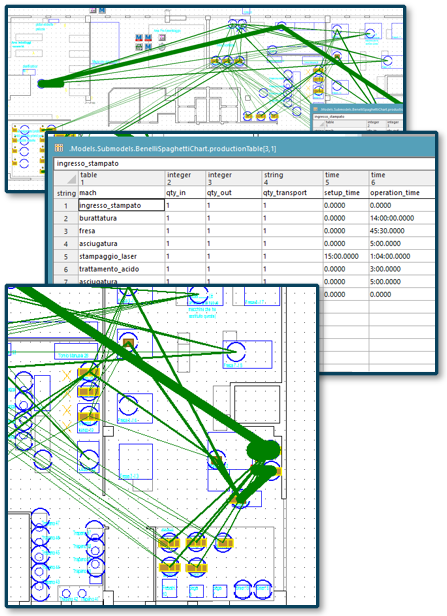
CASE 3) LIVE BIRD HANDLING
In the poultry industry, it is often necessary to determine the optimal combination of conveyor belt speed and the number of operators to achieve the best possible performance in the hanging area.
To address this need, I developed a simulation tool that allows all production parameters to be set and calculates the impact of these parameters on yield and productivity.
This simulator has proven to be more than just a consulting tool; it was provided to the client as a daily resource for calculating the efficiency of various production scenarios.
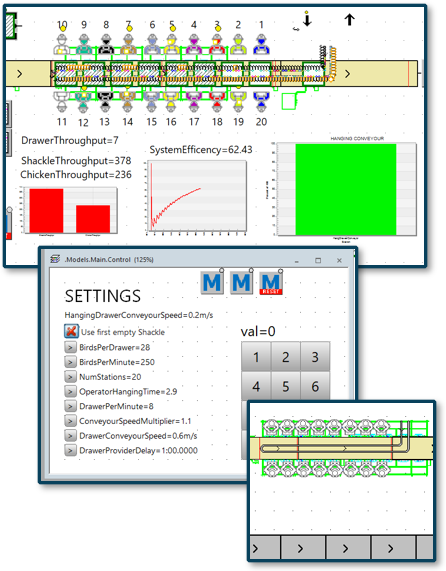