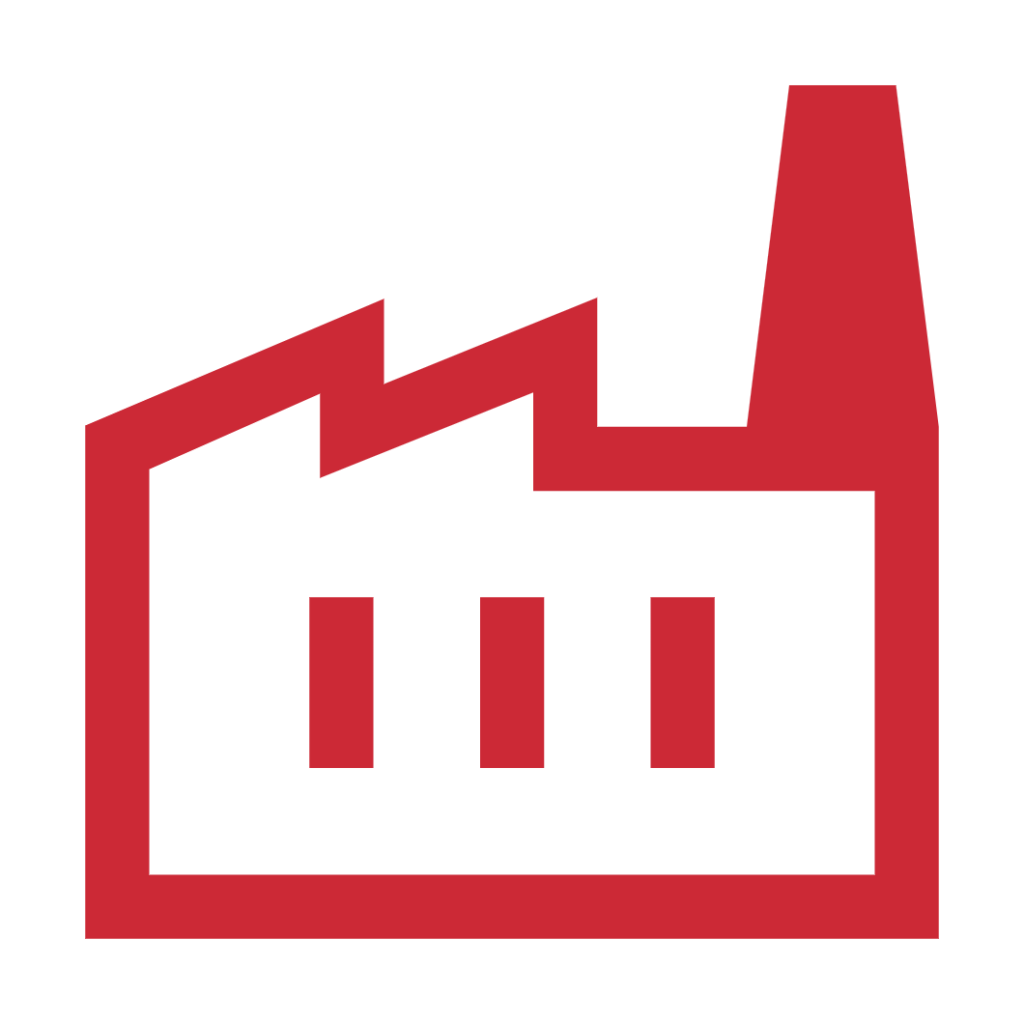
PLC Programming and industrial automation
I specialize in designing, implementing, and commissioning advanced PLC and HMI systems within Siemens or Allen Bradley environments. My work involves not only programming but also ensuring full integration and thorough testing for efficiency and reliability.
Beyond domestic projects, I have extensive international experience in commissioning, including on-site deployment, system fine-tuning, and customer support. Fluent in Italian, English, and Spanish, I effectively communicate with global clients and teams, focusing on troubleshooting and optimizing processes to boost efficiency and reduce cycle times.
I am fully available for business travel worldwide, committed to ensuring successful project execution and providing on-site support wherever needed.
I create HMI control panels that are user-friendly and visually appealing, making operations easier and reducing errors.
Additionally, I support plant design through formal analysis of operational cycles, drafting sequencers, flowcharts, and state machine diagrams to ensure optimized, scalable system design from the start.
CASE 1) INTERCOM (PRODUCTION OF POLYURETHANE AND NEOPRENE ADHESIVES)
For Intercom, a leading international company in the production of sprayable neoprene and polyurethane-based adhesives, I designed and fully implemented an entire manufacturing facility composed of nine distinct production islands.
The system enables the creation and production of complex recipes, along with the measurement and generation of quality certificates that include data on viscosity, temperature, and pH, all categorized by batch.
The supervision system, which I also designed and developed, is cloud-based, allowing the client to monitor production status remotely.
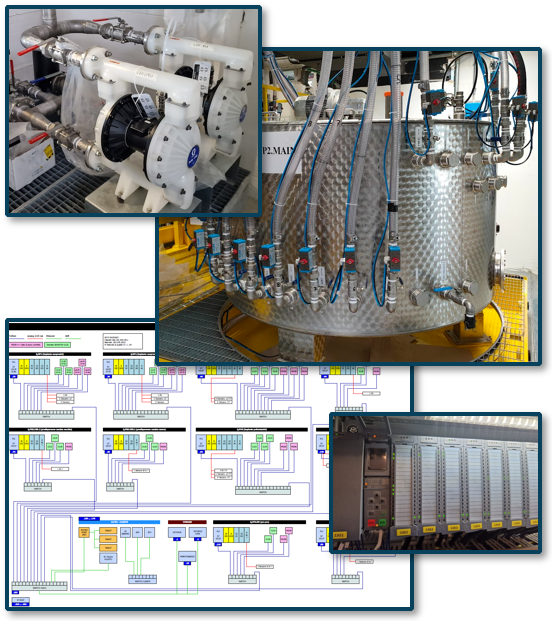
CASE 2) MEYN POULTRY MACHINERIES
I have personally been involved in teams responsible for the development, testing, commissioning, and on-site installation of the MEYN (formerly Maxitech) Maxiload TWIN system for live bird handling in the poultry market.
This highly complex system requires multiple teams for installation and startup. My primary responsibilities included the development and fine-tuning of specific program aspects, designing and optimizing HMI operator panels, as well as providing training and customer support for all installations of this system in locations such as Canada, the United States, Spain, and Israel.
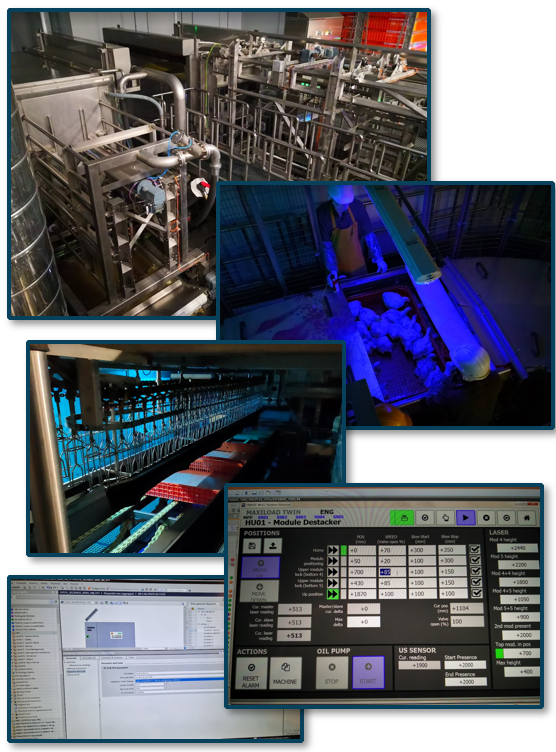
CASE 3) TNT EXPRESS
Fives is a French multinational company, with operations in Italy, and a leader in the production of transport systems for international logistics. In collaboration with Fives, I contributed to the development and commissioning of four transport systems for the express courier TNT (three in France and one in Norway).
My responsibilities included development, startup, testing, fine-tuning, customer training, and support during the initial phases of production.
The collaboration also extended to a third-party company responsible for the production of supervision systems and performance monitoring.
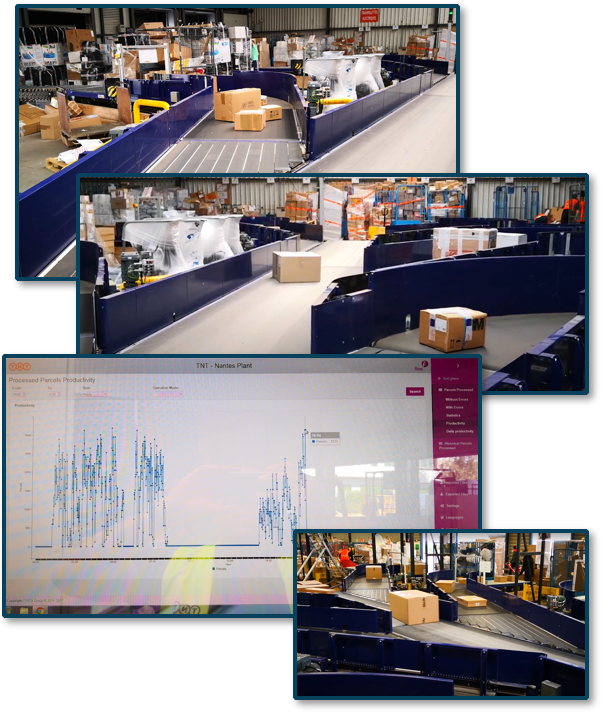