In today’s highly competitive industrial landscape, businesses are constantly seeking ways to optimize their processes and increase efficiency. One of the most powerful tools for achieving this is Discrete Event Simulation (DES). This simulation methodology allows industries to model and analyze complex processes, providing valuable insights into system behavior, resource utilization, and identifying potential bottlenecks. In this article, we will explore what Discrete Event Simulation is, how it works, and how its application in industrial settings can lead to significant process improvements, especially in the areas of bottleneck analysis and overall system efficiency.
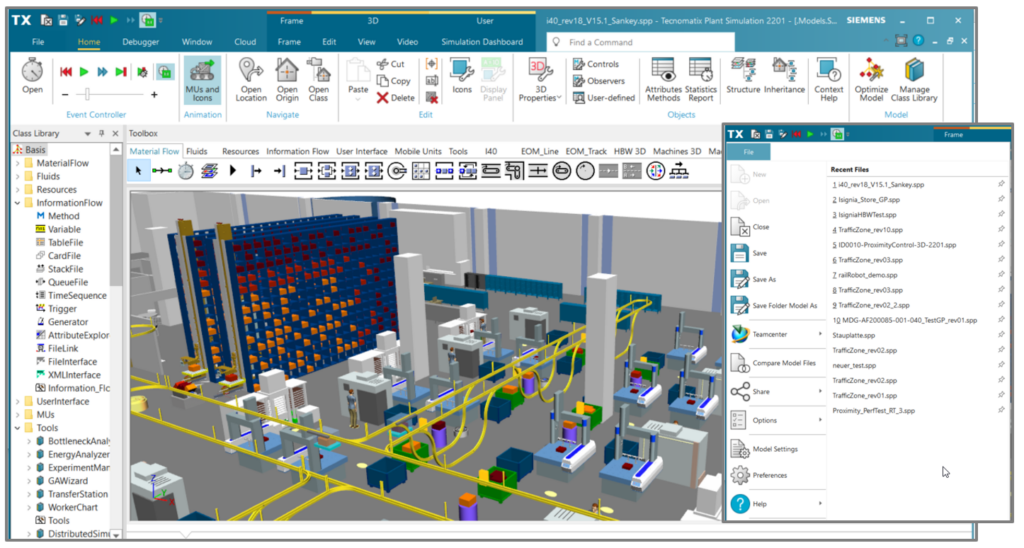
What is Discrete Event Simulation?
Discrete Event Simulation (DES) is a computer-based modeling technique used to simulate the operation of a system as a discrete sequence of events in time. In a DES model, the state of the system changes only at specific points, known as events. These events represent distinct moments in time when something important occurs that affects the system’s state, such as the arrival of a part at a machine, the start of a production process, or the completion of an assembly.
The core concept behind DES is that it does not track every moment in a system’s timeline, but instead jumps from one event to another. This makes it highly efficient for analyzing complex systems where continuous simulation might be computationally expensive or impractical. Each event in the simulation triggers a change in the system, and the state of the system is recalculated only when an event occurs.
The key elements of a Discrete Event Simulation model include:
- Entities: The objects that move through the system, such as products, customers, or machines.
- Events: The specific points in time when an action occurs that changes the state of the system (e.g., a machine starts operating, a part arrives).
- Resources: The assets required to process entities, such as machines, workers, or equipment.
- Queues: Places where entities wait when resources are not immediately available.
DES models are often used to analyze systems where timing and sequence are critical, such as manufacturing processes, supply chain logistics, and service operations. By simulating the flow of entities through the system and monitoring how resources are utilized, DES can provide insights into process performance and help identify areas for improvement.
The Importance of DES in Industrial Applications
In industrial settings, optimizing operational efficiency is crucial for maintaining competitiveness, reducing costs, and meeting customer demands. Discrete Event Simulation plays a key role in helping manufacturers achieve these goals by providing a framework for analyzing and optimizing their processes in a controlled, risk-free environment.
Some of the most important applications of DES in industry include:
1. Process Optimization
Manufacturing processes are often complex, involving multiple stages, resources, and interactions between different parts of the system. DES allows industries to model their entire production flow and evaluate the impact of various changes to the system, such as:
- Adjusting the number of workers or machines.
- Changing production schedules.
- Modifying workflows.
- Testing different inventory policies.
By running simulations, manufacturers can experiment with different scenarios and configurations without disrupting the actual production process. This allows them to determine the most efficient way to organize their resources and minimize waste, leading to higher throughput, lower operating costs, and better overall system performance.
2. Bottleneck Identification and Analysis
A bottleneck in a manufacturing system refers to a point in the process where work accumulates due to limited capacity, slowing down the entire system. Bottlenecks are a common problem in production environments and can significantly reduce the efficiency of the entire operation.
One of the most powerful applications of DES is its ability to identify and analyze bottlenecks in a system. Because DES models track the movement of entities through the system and monitor how long they spend waiting at each stage, it becomes easy to pinpoint where bottlenecks are occurring and what is causing them.
For example, a DES model might reveal that a particular machine is consistently overloaded, causing parts to back up in a queue. By experimenting with different resource allocations or process changes in the simulation, manufacturers can explore potential solutions to alleviate the bottleneck, such as:
- Adding more machines or workers at the bottleneck point.
- Reducing cycle times by improving machine performance or reducing setup times.
- Changing the sequence of operations to better balance the workload across the system.
By addressing bottlenecks, manufacturers can dramatically improve the flow of materials through the system, resulting in higher productivity and shorter lead times.
3. Capacity Planning and Resource Allocation
Capacity planning is another critical aspect of industrial operations. Knowing how many machines, workers, and other resources are needed to meet production targets without overinvesting in excess capacity is a delicate balancing act. Too few resources can lead to bottlenecks and underperformance, while too many can lead to unnecessary costs.
DES provides manufacturers with a powerful tool for evaluating different capacity scenarios. By simulating the production process under different conditions, businesses can gain a better understanding of how resource availability impacts system performance. This allows for more informed decisions about when to invest in additional capacity, how to optimize resource allocation, and how to adjust production schedules to maximize efficiency.
4. Supply Chain Optimization
In addition to improving internal manufacturing processes, DES can be applied to optimize supply chains. Manufacturing companies often rely on complex supply chains involving multiple suppliers, transportation networks, and distribution centers. Any disruption or inefficiency in the supply chain can have significant ripple effects throughout the production process.
DES enables businesses to model their supply chains and analyze how different factors, such as lead times, transportation delays, or supplier performance, impact overall system performance. By simulating different supply chain scenarios, manufacturers can identify potential vulnerabilities and develop strategies to mitigate them, ensuring smoother operations and more reliable delivery of products to customers.
5. Cost Reduction and Waste Minimization
Waste in the form of excess inventory, idle machines, or wasted time can be a significant drain on manufacturing profitability. DES helps identify areas of waste by simulating the flow of materials and resources through the system. For example, if a machine is frequently idle due to insufficient work in progress, it may indicate that the system’s workflow is not balanced correctly.
By simulating different production strategies, such as lean manufacturing techniques or just-in-time (JIT) inventory management, manufacturers can experiment with ways to reduce waste and streamline operations. The result is often lower operating costs, reduced lead times, and higher product quality.
Practical Examples of DES in Industrial Applications
Several industries have successfully applied Discrete Event Simulation to improve their processes:
Automotive Manufacturing
In the automotive industry, production lines are highly complex, with numerous components being assembled and tested at different stages. DES has been used to model the entire production process, allowing manufacturers to identify bottlenecks in assembly lines, optimize the use of robotic systems, and reduce downtime caused by machine failures.
Pharmaceutical Manufacturing
In pharmaceutical production, ensuring efficient use of equipment and meeting strict regulatory requirements are top priorities. DES has been used to model the production of drugs, helping pharmaceutical companies optimize batch processing, reduce cycle times, and improve overall equipment effectiveness (OEE).
Logistics and Warehousing
Logistics companies often rely on DES to optimize warehouse operations, from receiving shipments to packing and shipping products. By simulating the flow of goods through a warehouse, logistics companies can improve layout designs, reduce handling times, and optimize worker productivity.
Conclusion
Discrete Event Simulation is a powerful tool for industrial process optimization, offering a way to model, analyze, and improve complex manufacturing systems. Through its ability to identify bottlenecks, optimize resource allocation, and reduce waste, DES provides manufacturers with actionable insights that can lead to substantial improvements in efficiency, productivity, and cost savings. Whether applied to automotive manufacturing, pharmaceutical production, or logistics, DES has proven its value as a key component of modern industrial strategy, making it an essential tool for businesses seeking to stay competitive in today’s fast-paced market.